Common mistakes made when choosing a concrete coating
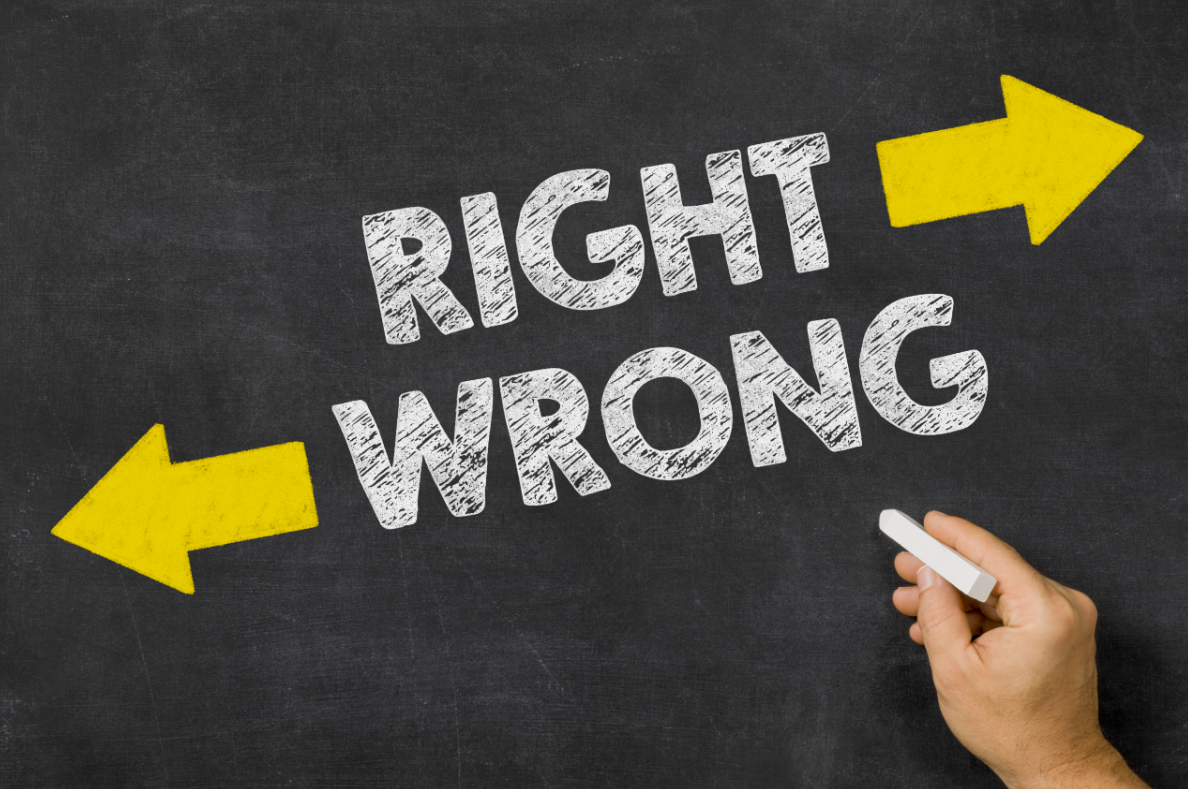
Save time and money on your next installation by avoiding these common mistakes people make when choosing a concrete coating solution.
Flooring and waterproofing
According to Chris Bauer, Head of Flooring at Hychem, the most common mistake found in Australian flooring and waterproofing applications is coating thickness being underspecified by site designers and engineers.
“We often come across coatings that have failed on job sites, simply due to the product being applied too thinly for its purpose. Therefore, it is not the product at fault, but rather the application,” says Mr Bauer.
Generally speaking, there are two kinds of concrete flooring and waterproofing protection products. The first kind is roller-applied and the second kind is trowel-applied, and each are designed for specific applications.
“Roller-applied products are to be cured at thicknesses between 0.1mm to 0.5mm.
“Due to their relatively thin application, roller-applied coatings should be used in low duty areas such as warehouses, storage, light duty manufacturing, domestic carparks and garages.
“Trowel-applied concrete coatings are designed to be installed at a thickness of 1mm to 10mm+, providing a much thicker and therefore more resilient concrete coating.
“Trowel-applied coatings are best suited to heavy duty areas such as commercial kitchens, food and beverage processing, heavy duty manufacturing and sports change rooms.
“When specifying a coating, it is imperative that environmental conditions and application specifics are fully understood to ensure the right coating is applied at the correct thickness.”
Hychem will carry out site inspections to recommend a suitable coating for new constructions, or will assess already damaged coatings to provide a recommendation for a suitable and hard wearing solution.
“As Hychem coatings are manufactured in Australia, they have been specifically formulated to suit our climatic conditions.
“It also means, for example, that if a product was required urgently but was not in stock, we could adapt an existing product, or seek to create an entirely new one,” says Mr Bauer.
Water and wastewater
According to Colin Murphy, Product Manager at Hychem, there is a common misconception that the term ‘epoxy’ refers to just one type of coating- one that is thinly applied, with a low resin content.
“This misconception is leading to coating failures right across the water and wastewater industries
“Coatings for concrete assets are used to prevent corrosion from harsh chemicals found at water and wastewater facilities, such as hydrogen sulphide and sulphuric acid. However, too often we hear that thin roll-coats of inappropriate epoxy resins have been applied in these highly corrosive environments and have failed very quickly.
“This leaves the impression that epoxy is useless in corrosion prevention when in fact there is a wide range of different epoxy coating options, each suited to different applications.”
Mr Murphy says that if applied at a sufficient thickness, epoxies of a high resin content have long term success at protecting concrete assets within harsh water and wastewater environments.
“Many believe that epoxies can only be roll-applied or trowel-applied, yet products such as Hychem’s TL5 is spray-applied, enabling a thickness of 2-6mm to be achieved.
“This gives TL5 the title of a ‘monolithic’ system, which means that (apart from a primer that is used occasionally), the epoxy is applied in one session at a high build thickness,” says Mr Murphy.
“Products that only require one spray-applied coating eliminate any intercoat adhesion problems.
“Products that require multiple coats have a much higher susceptibility to moisture and temperature damage during installation, affecting the adhesion between each coating layer. There is also a high chance of other contaminants getting onto the surface of the coating between the layers which can interfere with adhesion,” says Mr Murphy.
Mining
At ammonium nitrate storage facilities, it is a common problem that asset owners pay little attention to protecting the inside structure of their storage site, and instead, focus all their efforts on protecting the flooring.
“When moisture comes in contact with ammonium nitrate, nitric acid is formed. This results in the formation of nitric oxide gas which is highly corrosive to both steel and concrete. The gas is not always visible or noticed but can attack the structure of the storage site.
“Protecting the interior surface of the facility’s walls and ceilings from the start is equally as important as protecting the flooring,” says Mr Murphy.
In ammonium nitrate storage facilities, Hychem TL9 or TL6 can be easily applied to halt corrosion damage and keep the area protected in the long term. This will prevent costly repairs of the storage facility structure and overall safety of the site.
Across the board
Builders and designers using old or recycled coating specifications is a major problem across all industries.
“Whether it is within the grouting, flooring, mining or water industries, quite often clients ask Hychem to provide them with an equivalent product to one that has been previously specified for a job site.
“Quite often when we get to the specifics of the coating’s application, the product originally specified is unsuitable for the conditions.
“For example, we often will be asked to supply a double roll-applied coating for a sewage system but would never use a roll-applied coating of two coats – a single coating of spray-applied TL5 would be our only recommendation for effectively protecting the concrete.
“We would always suggest that designers and specifiers get in touch before they choose a coating. Old specifications may no longer be appropriate for the project, and as technologies are always changing, there may be a better, longer lasting solution,” says Mr Murphy.