Acidic by nature: sealing floors in a vinegar storage room
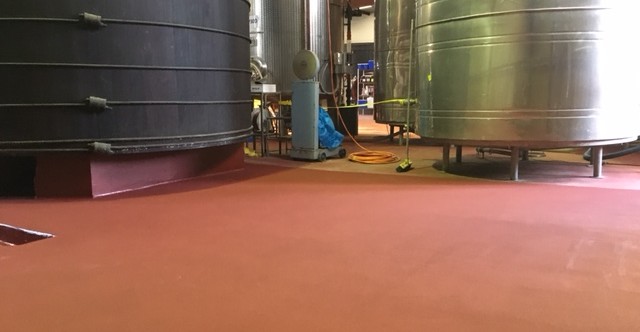
When contracted to provide a flooring solution for a vinegar storage room, Antiskid Industries needed to consider the nature of the product to ensure the most durable, effective solution. In assessing the challenge the space posed, Hychem’s Hycrete PU system was selected as the best solution.
What was the problem?
Concrete floors in food manufacturing facilities where acidic products such as vinegar are produced are particularly susceptible to corrosion. This is because the calcium contained in the concrete will be attacked by acids when they come into contact.
Vinegar contains acetic acid which is one of the strongest types of organic acid. When acetic acid makes contact with exposed concrete floors, they combine to form soluble compounds and leave exposed aggregate. If left unprotected the concrete floor will continue to erode, making it unsafe for any equipment such as tanks sitting on the concrete, as well as making the floor unattractive.
Very low levels of acetic acid (two per cent or weaker) will cause corrosion to occur, and as a regular bottle of household vinegar contains acetic levels around five per cent, it has a lot of potential to cause damage to exposed concrete.
Jamie Bailye, Business Development Manager at Antiskid Industries, said this potential acid contamination was the biggest challenge faced when choosing the right coating for the client.
“The intense acidity of the product packaged within the room and the likelihood of damage to the flooring substrate without an appropriate coating system meant that the client required a flooring solution that was extremely durable and would hold up against highly corrosive acids,” Mr Bailye said.
With an area of approximately 106m2, including a 13m bund wall of approximately 400mm in height, needing to be coated, Hychem’s Hycrete PU-SL and PU-TC were chosen to provide the client with the best outcome.
“As Hycrete PU products provide one of the best defense against chemical attack on the market and it is resistant to the chemicals found in organic acids such as acetic acid, it was determined to be the best fit for the client’s requirements and would offer the best value for money over the medium to long term,” Mr Bailye said.
Applying the coating
The total application took approximately four days and the entire area had to have any acidic content present neutralised prior to installation to ensure maximum bond and long lasting durability.
“There were also significant concrete substrate repairs and the area had to be scabbled to remove eaten concrete,” Mr Bailye said.
Once the surface preparation was complete, Antiskid installed a poly/cement floor screen to build up the floor and infill low areas to a nominal thickness of 12mm. Next Hycrete PU-SL was applied at a 6mm thickness in a slip resistant finish.
“We then applied Hycrete PU-TC, which is a top coat, to seal the coating and provide extra chemical and slip resistance. One of the benefits of this product was its ability to be customised to a range of colours, so we were able to colour match the product to the existing brick red colour,” Mr Bailye said.
“We also re-graded the spoon drain to improve water falls to waste and create a smooth finish.
“The client was very happy with the overall job and the finished product.”