Reducing the risk of concrete coating failure
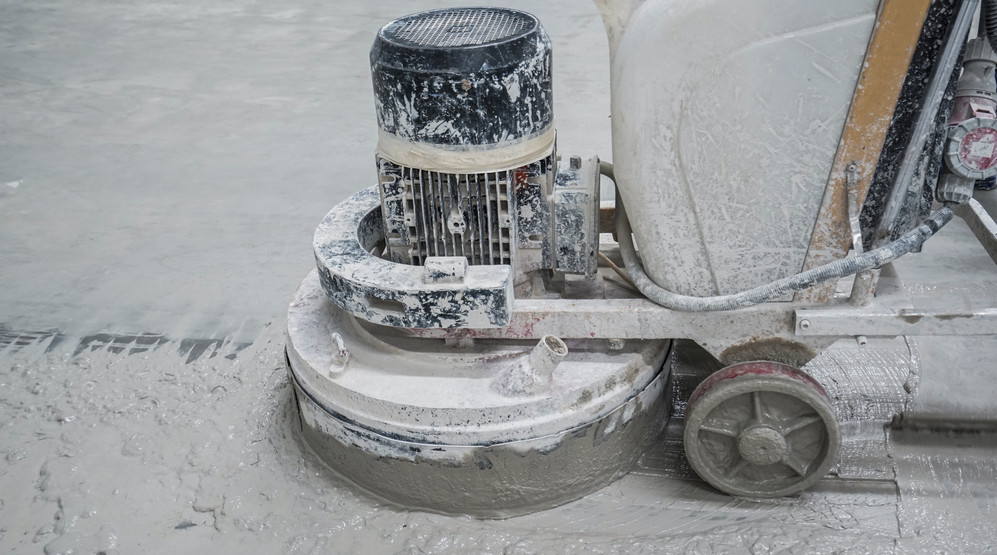
Concrete coating failure occurs when the coating separates from the concrete surface, causing cracking, flaking and bubbling. Not only will this prevent the coating from protecting the concrete which leads to deterioration, but this also causes the surface to become unattractive and at worst it can cause health and safety issues. Here, we look at three key factors that affect the success of a coating, and the steps to take to avoid coating failure.
Moisture transmission
Moisture levels of concrete substrate is one of the most common causes of coating failure. Particularly, the process of moisture transmission – where water vapour rises to the surface of the concrete due to changes in environmental temperature and humidity – is a major problem.
Chris Bauer, Head of Flooring at Hychem said, “Moisture content is an important factor to consider when installing a coating. However, a lot of epoxy coatings can tolerate high moisture content in the concrete substrate and can still be applied without problem. What really needs to be considered is the movement of moisture known as moisture transmission that can cause bonds to fail months or years later.”
There are various moisture and humidity tests than can be undertaken to evaluate moisture content and the rate of moisture transmission such as relative humidity tests and calcium chloride testing. Once the level of moisture has been established, a more breathable coating or a suitable primer can be applied to reduce the chance of coating failure.
Surface preparation
Another cause of coating failure is improper surface preparation.
In order for the coating to adhere completely to the concrete, the surface must be cleaned and roughened, through techniques such as diamond grinding or sand blasting, to remove any contaminants such as oils, dirt or loose materials that could affect adhesion.
Micro-cracks and other defects on the surface should also be repaired to decrease the chance of moisture getting between the surface and the coating.
“Correct surface preparation is vital to the success of a coating installation. Removing contaminants and repairing surface defects will ensure that the coating can properly adhere to the concrete,” Mr Bauer said.
Application
Different coatings require different levels of thickness and application techniques to ensure a successful coating installation.
If a coating is applied under the minimum required thickness, the physical properties of the coating are compromised, making the coating highly susceptible to cracking and deterioration.
However, applying the coating at a thickness above the maximum specification can not only cause it to become aesthetically unattractive due to wrinkling and running, but it can also cause issues during the curing process which could lead to blistering.
Mr Bauer said disproportionate mixing of the epoxy can also increase the chances of bond failure.
“Epoxy coatings come in one or two part systems that need to be mixed at the appropriate ratio or a wide range of defects could occur. This could include compromised durability and weight tolerance as well as in extreme cases total coating failure.”
Experience matters
According to Mr Bauer, selecting an applicator that understands the various factors that can result in coating failure and has the knowledge to suggest the best options to prevent this is key to a long-lasting coating.
“Hychem has a strong and trusted network of trained applicators throughout Australia,” Mr Bauer said.
“Our applicators all have extensive experience in the flooring industry, and are able to advise clients on what will work best for their floor to ensure the coating is successful in the long term.
“Our contractors are ready to take on new projects in all cities and all states.”