Industry demand drives product development
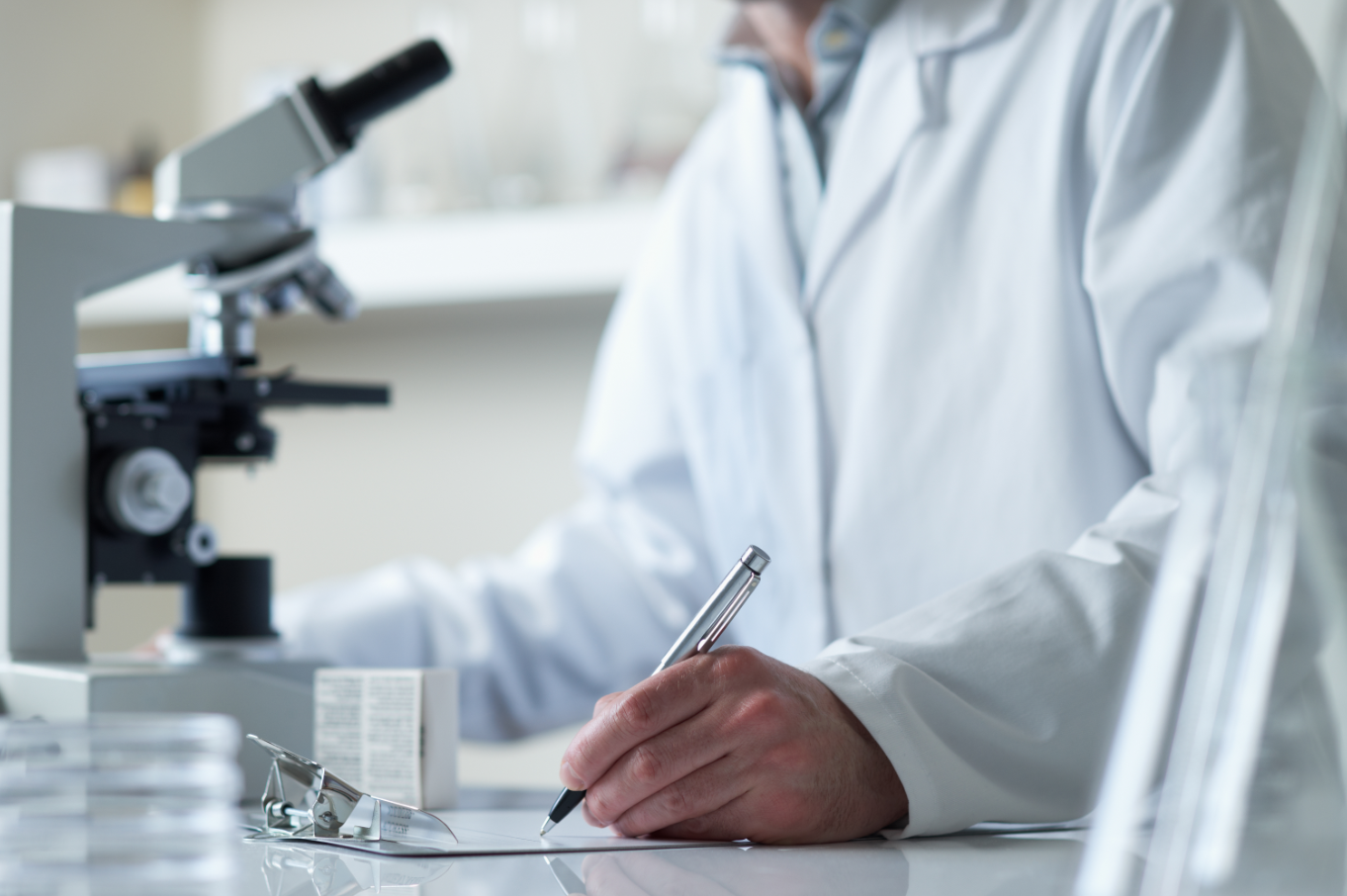
Interview with Raj Velayutha, Technical Manager Product Development
Keeping new product development in line with industry demand requires out-of-the-box thinking as well as a keen understanding of what customers want. By tailoring existing products to meet ever-changing customer needs, demand in fact becomes a positive instigator of product innovation.
What are current demands for new products?
Workability and fast cure
At the moment, there is particular demand in concrete coating for products with a long pot life and a short cure time.
Contractors and architects are looking for coatings that can be workable for long periods of time, allowing them to apply the coating before it starts to set, but are also looking for products that are able to cure quickly so that the coated area is ready for use by the following day.
This is a great challenge as these qualities are directly proportional to one another. We really have to think outside the square to come up with materials that are workable while being inversely proportional.
This involves sourcing additives that have two parameters – one that slows down the process and one that speeds it up, while also ensuring that the end product is strong enough, matches the surface texture and is easy to apply.
Greater flexibility
Greater flexibility for epoxy resin based coatings is another demand we receive from asset owners and contractors, especially for surfaces such as concrete and metals exposed to various immersion conditions or structures located outdoors.
The changes in outside temperature can cause the concrete to expand and contract, which over time can lead to cracking of typically used epoxy resins. Materials with increased flex, yet a rigid and hard-wearing finish must then be incorporated into the solution, again ensuring that all other criteria such as long-life, ease of installation, cost and strength are all accounted for.
Corrosion resistant and non-toxic
Within the water and wastewater industries, water authorities require anti-corrosive and non-toxic solutions that do not change the quality or taste of the contained water. Australian standards such as the ‘AS 4020:2005: Testing for products for use in contact with drinking water must be adhered to. This is the case for Hychem’s TL5 range and the TL6 roll coat which are certified for use in potable water.
For structures that come into contact with wastewater, resilience to highly corrosive chemicals and solvents is the main coating characteristic required.
At the moment, we are in the final stages of developing an enhanced TL5 product for coating of assets within the water and wastewater industries. The new TL5 IRF has incorporated special resinous materials to enhance the product’s flexibility.
This makes this particular formula a cross-breed between the composite industry and the building and construction industry. It combines strength and corrosion resistance with high flex and short cure properties. To my knowledge, this combination of materials has never been attempted before in the coatings industry, but has so far been successful as it also has excellent acid resistance for long periods of time.
Steps from initial idea to new Hychem product?
Developing a new or enhanced product involves a lot of design work and testing. Typically a new product idea would go through the following phases of development:
Theoretical design
As the first step in development, theoretical design involves looking at the chemical structure of a range of materials to select those that might be suitable for the desired requirements.
Sometimes the chosen materials look good on paper but have limitations once you see them in real life, such as high odour. If this happens, we need to go back to the drawing board and search for something different.
Bench work, testing, refinement
If materials pass the first phase of bench work and testing, they move onto refinement, validation and lifecycle tests. If a product fails, we must start again from scratch.
Prototype
Once we are reasonably confident that our selected materials will be successful, we then weather-test this solution on a concrete slab or a cast specimen. If this is successful, we then make up larger samples to send to representatives for field testing.
Secondary testing, refinement and validation
Result of the field tests are then taken into consideration and the solution is adapted accordingly. It is then tested once again to ensure that all field requirements have been met.
Product documentation
Once sufficient testing has been carried out, and the solution has been deemed successful, we then freeze the formula and documentation work can begin. Emissions levels and ease of installation are all looked at, while documentation including Technical Data, Material Safety, Quality Assurance tests as well as application guidelines and marketing information are all generated.
European Union Registration, Evaluation, Authorisation and Restriction of Chemicals (REACH) requirements must also be met. These addresses the production and use of chemical substances, and their potential impacts on both human health and the environment.
Following a cost appraisal to match market requirements, labelling and packaging is then designed for the product before it is ready to be released.
What factors must be considered when creating new products to suit Australian conditions?
Each new product must meet all local regulations, including occupational health and safety requirements and be suitable for Australia’s different climatic conditions.
Consistent product performance across temperatures ranging from 10°C to 40°C is also a specific consideration for Australian conditions. This involves cold climates in Tasmania and alpine areas to excessive heat throughout most of Australia in the summer months.
Where does Hychem source its materials?
At Hychem, we have good relationships with a wide range of trading houses from which we can source materials. We only seek materials of the highest quality, and typically select those from either Europe or North America.
How does Hychem stand out from the crowd in overall innovative product development and design?
Hychem’s understanding and success within the Australian construction resin market over the company’s 29-year long history makes us a well-rounded and knowledgeable team.
Our dedication to quality and rigorous product testing, both in the lab and out on the field before market release, is what makes our range so successful.
In the case of the new TL5 IRF, the freedom that Hychem allows for our team be innovative has led us to bring together a previously unused combination of materials to produce a hard-wearing solution. This new technology could pave the way for the next generation in anti-corrosive coatings for the water and wastewater sectors.
How does Hychem communicate with its customers and the industry to understand their needs and ‘foresee’ their requirements?
Colin Murphy, our product manager at Hychem has regular meetings with key engineers to discuss current requirements and new innovations. This gives us clear insight into the market and the ability to foresee future product demand.
Our development team also has regular visits to site so that we can grasp a close understanding of each application, to then translate this into our product design.
Once a new product has been released, Hychem then showcases each product at national conferences and exhibitions to gauge interest and attract new users of the product.