Preventing infrastructure failure in the water industry
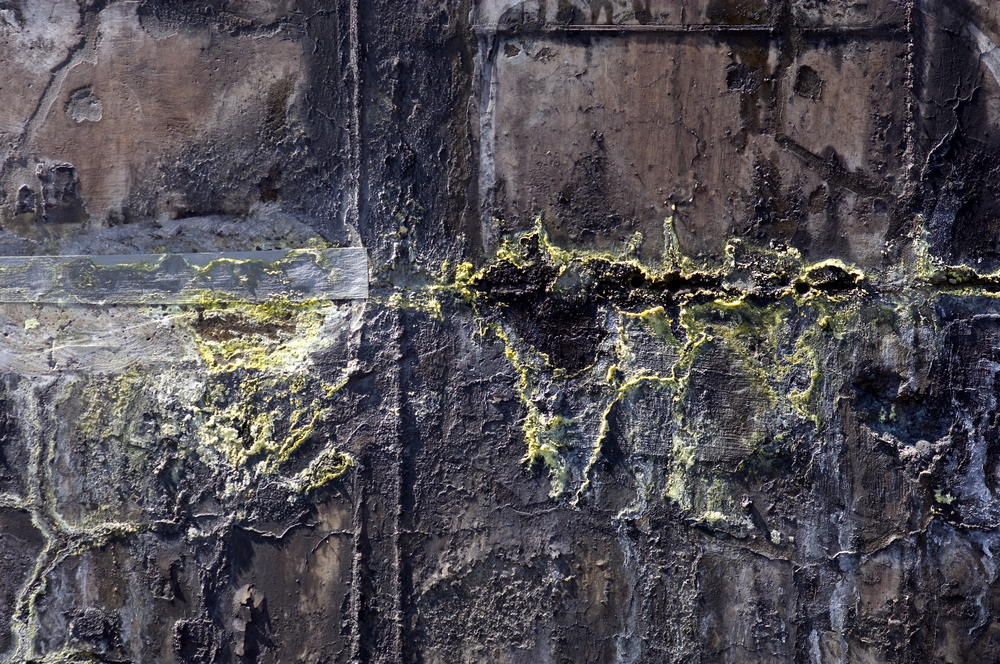
Corrosion of water infrastructure in Australia costs the economy around $983 million per year, which is around $60 for every adult in the country. While it’s a massive problem for the water industry, there are some cost reduction strategies that utilities can implement to prevent damage. Here we look at one of the key areas to consider, epoxy coatings.
The report comissioned by the Australiasian Corrosion Associtation (ACA) looks at the cost of corrosion in all aspects of the water industry, from pipes and treatment facilities, to manholes, sewer vents, tanks, reservoirs and pumping stations. In particular, it notes that costs are higher for infrastructure that deals with sewage, as regular maintenance and repair is required due to the presence of hydrogen sulphide which forms corrosive hydrosulfuric acid when mixed with water.
When failure of a water asset occurs it has varying economic impacts. For example, the failure of a major pipe could impact the surrounding area and have long-term consequences on water and wastewater pipes servicing urban centres. The cost of repair or rebuilding would also be high.
Epoxy liners provide a solution
According to Colin Murphy, Product Manager for Hychem, epoxy coatings can provide a number of cost reduction benefits which water utilities have started to take notice of.
“When looking for ways to reduce the cost of corrosion on water infrastructure assets, utilities should consider epoxy coatings as part of their corrosion management strategy. We have worked with a number of water utilities that have been impressed with the long-term performance of epoxy coatings in their systems,” Mr Murphy said.
Long lasting
Epoxy coatings are an ideal solution for the protection of water infrastructure due to their chemical resistance, making them long-lasting. In contrast, CAC mortars, for example, are not as durable in harsher water and wastewater environments as it will corrode over time depending on the level of hydrogen sulphide it is exposed to.
“Products like Hychem’s TL5 has had 20 plus years of 100 per cent success and with minimal change to the lining,” Mr Murphy said.
“For utilities looking to reduce the costs of managing corrosion and preventing failure in their systems, this is an attractive option as it provides long-lasting protection. This can save utilities long-term maintenance costs as they do not need to carry out regular repairs to the infrastructure.”
Reducing downtime
One of the cost factors that utilities need to consider is the cost of shutdown and the disruption this can cause to communities.
“TL5 is one of the easiest coatings to work with and apply. It can be spray applied to a thickness of up to 6mm, which means only one application is needed. Other coatings need to be reapplied two or three times before they reach a suitable thickness,” Mr Murphy said.
“As TL5 can be applied in one coat it has the major benefit of providing a complete seal relatively quickly which reduces the amount of downtime required. For critical infrastructure this is important as it can be up and running again in as little as six hours.
“Furthermore, the single coat application addresses adhesion problems that are associated with two-part epoxies.”
Rehabilitation versus rebuilding
With the cost of rebuilding water infrastructure greater than rehabilitation, epoxy coatings provide utilities with a cheaper, long-term option.
“The true benefit of TL5 is that it is purposely designed for the water and wastewater industries, and has been tested for over 20 years in the harsh Australian climate,” Mr Murphy said.
“Not only can it prevent acid corrosion when installed at a new facility, it can also halt corrosion damage on an existing asset.
“This means water utilities can extend the life of their assets and greatly reduce the chance of failure and the need to rebuild.”